Life in the field experimentation team
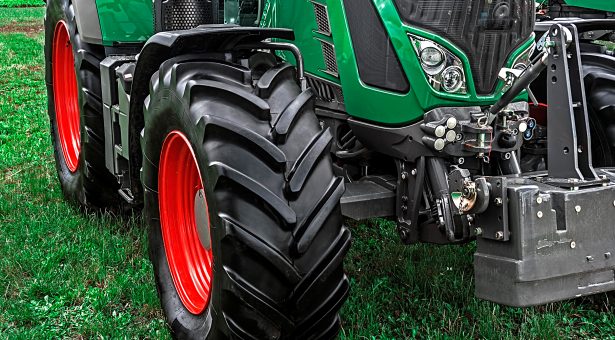
By Richard Samworth.
I work in the field experimentation team, which is responsible for looking after all the plants which are grown outside, i.e. not in the greenhouses or the controlled environment rooms at the John Innes Centre.
It’s farming but on a smaller, very accurate, scale.
Including myself, there are 5 of us in the team, plus our manager, Cathy Mumford. Chris and I generally do the machinery work. Then there is Kevin, who primarily looks after the pea cage, and Stephen. We also have an apprentice; Luke, who was recently awarded the Intermediate Agriculture Apprentice of the Year 2017 by Easton and Otley College.
We mainly deal in cereals, although we also have a small oilseed rape trial, so we’re also lucky in that we tend not to have different harvesting times.
We grow wheat, barley, peas (in the ‘pea cage’) and work on a few Genetically Modified (GM) potato trials and oil seed rape.
The only GM crops we grow are on-site in the bespoke caged area, no GM crops are grown at Church Farm or at Morley.
We cover the field experiments on-site at the Norwich Research Park, as well as our sites at Church Farm in Bawburgh and our partnership fields, which are 10 miles away in Morley, where the land is a little more consistent than we have here, but the downside is the increased distance from the laboratories.
The new field experimentation facility at Church Farm will change all of that, and allow the scientists to benefit from facilities and fields that are side-by-side.
The new facilities at Church Farm will save us a lot of time. Not only in terms of travelling time, but even in finding the equipment we need.
At the moment we have a portacabin, two shipping containers, the goods yard, the farm at Morley, a store cupboard on-site and Church Farm across which all of our equipment is distributed. It can be very frustrating when you need a specific piece of kit, but don’t know which of those places it was needed in last.
Having a single barn at Church Farm, close to where the equipment will be most frequently needed, and where everything will be accounted for in a structured way, will be lovely. Plus, we won’t need to keep driving backwards and forwards between the sites, which will lower our diesel costs and emissions.
We don’t cover large areas. All of our machinery is plot size. Even our tractor is a small tractor, compared to commercial farmers. We still have busy periods around harvest time and drilling, just like commercial farms, but because of the scale of what we’re doing, our busy times aren’t as long as commercial farms.
However, because of the accuracy required for what we’re doing, it takes us much longer to cover a smaller area than commercial farmers – they can do in one pass, an area it might take us a day to do as we’re working on individual plots. We have to drive through the plot, pause, process it through the combine and then drive through the next plot, pause and process it etc etc.
Our tractors and sprayer are fitted with auto-steering and GPS location, which means we can be accurate to within 2-3cm. You can then come back to a field 3 years later (theoretically) and know exactly where you were and what you did previously. Although as with sat navs the system does occasionally have a blip.
The machinery allows us to plan exactly which trials are taking place where, so we can be flexible with timings and accurate in planting the seed, so that it’s ready to go where it needs to go.
Planning which experiments are taking place and where is one of the biggest challenges we face each year. This is because, different experiments have different requirements in terms of plot location, size, watering, sunlight and treatments etc.
All the planning of what is being done and where, is done via Cathy Mumford. Project Leaders and their teams will go to Cathy before each season and let her know what they need and she will attempt to fit all those puzzle pieces together into the field, bearing in mind what has been grown on that land in previous years. All of which needs to be planned as far in advance as possible.
During harvest time we all come together and the trials need to be harvested and collected into small bags. Myself and Luke drive the combines, which do weights and moisture readings.
Once we have finished harvesting Stephen and Kevin can crack straight on with processing, which involves cleaning and dressing the seed. While they do that, myself, Chris and Luke will be out preparing the land for drilling season, so our work does follow commercial farming cycles.
As well as the farming side, we do a fair amount of work around the institute, although we now share this with the Norwich Research Park team.
We’re currently responsible for gritting the site for example. We take our lead on when to grit from Norfolk County Council’s gritting team, as they have access to a range of weather data which informs their plans, if they are gritting we will grit. We also have a couple of snow ploughs, which we’ve had to use this year to clear the site.
My background is in engineering and I’d never been in a tractor before I joined the John Innes Centre.
I spent 10 years working in a factory as a machine setter, making turned parts for the aeronautical and automobile industries, so this has been a big career change for me. After I decided to leave engineering, I worked as a landscaper for a few years. Shortly afterwards the John Innes Centre were looking for casual staff to help out in the greenhouses, so I worked with the Hort Services team, before being asked if I’d be interested in driving the tractor during harvest time. I haven’t looked back since.
I really enjoy what I do, because it is varied, at least in in a seasonal way.
My favourite thing about my job is operating the machinery and seeing the tangible effects of what we do. For example, once the trials start to come through a few weeks after drilling and they are all in perfectly straight lines, it`s satisfying to see everything neat and where it should be.
With my engineering background, I recently took the opportunity to do a welding course. We have a little stick welder, so I do a few maintenance jobs over winter, to make sure we’re all ready to go again when the weather improves.
Because the type of work we do here is so unique, it’s useful to have the ability to build or modify little bits and pieces of equipment to make our lives easier and the service more efficient. If it then doesn’t quite work we haven’t spent £100s commissioning somebody to do something. Instead it’s all done in-house.